Overview
The 5-day Lead Auditor training course aims to provide participants with the knowledge, and develop the skills and expertise necessary to:
-
Audit a Quality Management System (QMS) based on ISO 9001:2015
-
Ensure that the organization is competent in maintaining and continually improving its QMS
-
Perform third party audits by applying widely recognized audit principles, procedures and techniques
-
Proficiently plan and perform internal and external audits in compliance with ISO 19011 and the certification process according to ISO 17021.
-
Manage audit teams and audit programmes, communicate with customers, resolve conflicts, etc.
Based on practical exercises, the participants will master the audit tools and techniques.
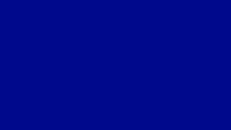
ISO 13485: 2016
Lead Auditor


First time you visit our website?
​
Empower Your Team with Industry-Leading Training Programs
Tailored corporate training for leadership, technical skills and professional development
​
-
We serve corporate clients investing in peoples' knowledge, skills, and competencies, to improve business performance, enhance process, product and service quality, and achieve sustained growth and profitability.
-
We understand the meaning of the business terms "Voice of the Customer" and what constitutes "value" from the customer's point of view.
-
We also understand the difference between "value" and "waste" from the business and individual learner point of view.
-
-
We care about the people, the knowledge enhancement of which is entrusted to us by their organisation or themselves.
-
We focus on learning (not just on training, and issuing certificates) and providing post-training advice and support through workshops and consulting services.
Stratos Lazaridis
CEO The Marvel Academy
Corporate Training Solutions
Mob: +44 (0)749 114 7156
Contents
-
Overview
-
Course purpose
-
Who should attend
-
Learning objectives
-
Course agenda and content
-
Prerequisites
- Training approach
- Examination
- Certification
-
General course information
​
​
Lean Champion
​​Overview
​
The 1-day training course is designed to provide the basic knowledge and skills required for individuals who are candidates for the role of the Lean Champion.
Organisations adopting Lean and aspiring to become Lean Enterprises are often driven internally by a dedicated Lean Champion.
This role is typically assigned to someone who exemplifies the drive, leadership, training, and commitment to:
-
Lead a company aiming to improve the organization’s operational performance
-
Increase total customer satisfaction.
Lean Champions:
-
Are often the most critical element of a successful Lean deployment initiative, providing the knowledge, vision and dedicated focus required to maintain a continuous improvement environment.
-
Typically have varied responsibilities and can come from different areas of the organization, which includes a role within the company that represent the operational side of the business.
​
It is not uncommon to find a vice-president or Senior Manager spearheading the organization’s Lean deployment efforts; however, often Champions come from the middle management or Supervisors in the organisation adopting Lean.
​
​​For more information about the role of the Lean Champion please click here.
​
Course Purpose
​
Training focuses on team building, basic project management and conflict resolution to ensure that delegates are capable of:
-
identifying Lean waste (muda)
-
Identifying the root causes creating the waste
-
Finding and and prioritising opportunities to eliminate or reduce the above root causes
-
Consistently delivering significant improvement results through guiding, coaching and enthusing colleagues.
​
Who Should Attend
​
The course is aimed at individuals whose role includes tactical Lean leadership responsibilities, including Lean Facilitators or Lean Champions with responsibility for governing/ overseeing Lean projects.
​Learning Objectives
​
By completing this course, delegates will be capable to:
​
-
Explain to Lean team members:
-
The 5 principles of Lean Thinking
-
The benefits deriving from their application across the organisation
-
What is customer, value, and waste
-
How to differentiate between the three types of value: CVA, BVA, and NVA
-
​The three MUs in Lean: Muda, Mura, and Muri
-
​
-
How to identify areas for improvement through:
-
Regular Gemba walks and the application of the "process stapling" technique
-
The creation and analysis of process maps and value stream maps
-
​
-
How to:
-
identify the eight types of Lean waste (muda)
-
identify the root causes creating waste by performing root cause analysis (RCA)
-
Assess risk, plan, pilot, and implement solutions to eliminate or reduce the root causes
-
Communicate effectively improvement results to senior management.
-
​
Course Content
​
-
Lean roles and responsibilities
-
Understanding the role of Lean Champion and the associated skills and attributes
-
Change management
-
Dealing with the culture change when adopting Lean
-
Resistance to change
-
Conflict resolution
-
​
-
Lean project management process
-
Lean project selection and commissioning
-
Setting up the project
-
Determining the current process state (AS-IS)
-
Designing the improved process state (TO-BE)
-
Implementing the process changes and standardising the improved process
-
Training people in the improved process
-
Handing over the improved process to BAU operations
-
Benefits realisation
-
​
- Lean principles: understanding
- Why the adoption of Lean Thinking is important to the business and its stakeholders
- How deployment of Lean across the organisation benefits the business
-
Basic Lean tools and techniques:
-
Visual management system (visual workplace)
-
Displays, controls, and KPIs
-
Measures vs. targets/ KPIs
-
How to determine, measure, and monitor the effects of waste reduction
-
​
-
Process mapping
​
-
Value stream mapping
​
-
The 3 MUs of Lean: Muda, Mura, and Muri
-
The eight types of Lean waste (muda)
-
​
-
Root cause analysis
​
-
How to reduce Lean waste
​
Prerequisites
​
Proficiency in the English language, willingness to learn, and open mind to new ways of working.
​
There are no pre-requisites for this course. However, to gain maximum benefit from the course, delegates should have some existing knowledge of Lean. This could have been gained from attending a course in Lean awareness, or Lean Six Sigma White Belt, or introduction to Lean.
​
Training Approach
​
The course covers both theory and practice:
-
Slide-based training sessions, supported by examples
-
Preparation for the Foundation exam
-
Practice test (mock exam) simulating the certification exam.
​
Examination
​
There is no scheduled exam for this training course.
​
Certification
​
Delegates attending the course will be issued with a certificate of attendance.
​
General Course Information
​
For general course information please click on the link here.
​
N.B. Please read our Terms & Conditions (T&Cs) and ask for clarifications, if any, before booking your training event.
​
Book now to reserve an on-site or online instructor-led training event of your choice.
​
For more details about our:
-
List of training courses please click here.
-
Consulting services please click here
-
Workshops please click here.
​
For queries, including non-obligation quotes, please contact us.
​
​
Training Course details
-
1 day (09.00 - 17.00 GMT)
-
Online instructor-led via zoom.us
-
£350 + VAT
-
Deadline for payment/ registration: 2 calendar days before course start
-
Included: 1 day online instructor-led training, delegate workbook, online exam, and certificate.
​
