Overview
The 5-day Lead Auditor training course aims to provide participants with the knowledge, and develop the skills and expertise necessary to:
-
Audit a Quality Management System (QMS) based on ISO 9001:2015
-
Ensure that the organization is competent in maintaining and continually improving its QMS
-
Perform third party audits by applying widely recognized audit principles, procedures and techniques
-
Proficiently plan and perform internal and external audits in compliance with ISO 19011 and the certification process according to ISO 17021.
-
Manage audit teams and audit programmes, communicate with customers, resolve conflicts, etc.
Based on practical exercises, the participants will master the audit tools and techniques.
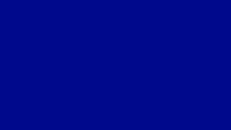
ISO 13485: 2016
Lead Auditor


First time you visit our website?
​
Empower Your Team with Industry-Leading Training Programs
Tailored corporate training for leadership, technical skills and professional development
​
-
We serve corporate clients investing in peoples' knowledge, skills, and competencies, to improve business performance, enhance process, product and service quality, and achieve sustained growth and profitability.
-
We understand the meaning of the business terms "Voice of the Customer" and what constitutes "value" from the customer's point of view.
-
We also understand the difference between "value" and "waste" from the business and individual learner point of view.
-
-
We care about the people, the knowledge enhancement of which is entrusted to us by their organisation or themselves.
-
We focus on learning (not just on training, and issuing certificates) and providing post-training advice and support through workshops and consulting services.
Stratos Lazaridis
CEO The Marvel Academy
Corporate Training Solutions
Mob: +44 (0)749 114 7156
The Framework of Lean Kaizen for Business Problem-solving
​
Introduction
Kaizen:
-
Is the Sino-Japanese word for "improvement".
-
Is a Lean concept referring to business activities that continuously improve all business functions
-
Involves all employees at all organisational levels, from the CEO to the assembly line workers.
Kaizen applies to:
-
Business processes, such as purchasing and logistics, that cut across organizational boundaries into the supply chain
-
Disciplines such as Information Technology, accounting, healthcare, psychotherapy, life coaching, government, and financial services.
Kaizen aims to:
Relentlessly seek for, identify, and eliminate Lean waste (muda, mura, and muri) in all its forms (there are 8 wastes in lean, abbreviated by mnemonics/ acronyms, such as TIMWOODS and DOWNTIME).
Kaizen:
-
Was first practised in Japanese businesses after World War II
-
Was influenced, to an extend, by American business and quality-management subject matter experts, such as Edward Deming, and teachers, (senseis) most notably at Toyota (refer to the Toyota Production System (TPS) and the Toyota Way
-
Has spread throughout the world
-
Has been applied to environments outside business and productivity.
​
Overview
​
The Japanese word Kaizen:
Means "change for better"
-
Has no inherent meaning of either "continuous" or "philosophy" in Japanese dictionaries and everyday use.
-
​Refers to any improvement, one-time or continuous, large or small, in the same sense as the English word "improvement".
However, given the common practice in Japan of labelling industrial or business improvement techniques with the word "Kaizen", particularly the practices spearheaded by Toyota, the word "kaizen" in English is typically applied to measures for implementing continuous improvement, especially those associated with a "Japanese philosophy".
Two common approaches of practising Kaizen are the "point Kaizen" and "system Kaizen.
​
Point Kaizen
​
This approach:
-
Is the most commonly implemented type of Kaizen.
-
Involves rapid action, usually without much planning.
-
Is applied as soon as something, such system, piece of equipment, etc. is found to be broken or incorrect
-
It involves immediate actions taken to correct the identified problem/ issue.
​
The above measures:
-
Are, generally, small in terms of size/ have limited scope of application
-
Are taken in isolation and are easy to implement
-
May have significant positive effect in containing or fixing a problem requiring immediate action.
​
In some cases, it is possible that the positive effects of point kaizen in one area can can be replicated to reduce or eliminate issues in other areas.
Example of point kaizen: a Supervisor conducting an inspection, may find a number of issues, and he may ask the person responsible for the inspected area to, e.g. perform a point Kaizen (5S) to rectify those issues.
​
System Kaizen
​
System Kaizen is:
-
Performed in a timely and organized manner
-
Scheduled to address system-level problems in an organization.
-
Higher level strategic planning method, compared to point Kaizen, implemented within a short period of time.
​
Characteristics of the Kaizen Problem-solving and Continual Improvement Framework
​
Kaizen is a daily process:
-
Its purpose is beyond simple productivity improvement.
-
When it is practised correctly, humanizes the workplace, and eliminates overly hard work (muri)
-
It teaches people how to perform experiments in their own area of responsibility using the scientific method
-
It also teaches how to identify and eliminate waste in business processes.
Kaizen takes a humanized approach to workers and to increasing productivity:
-
The idea is to nurture the company's people as much as it is to praise and encourage participation in Kaizen activities.
-
Successful implementation requires "the participation of workers in the improvement. People at all organizational levels should be practising Kaizen, from the CEO down to janitorial staff, including external stakeholders, such as suppliers, when applicable.
Although Lean Kaizen is commonly associated with manufacturing operations, as at Toyota, it has also been applied in non-manufacturing environments.
-
The format for practising Kaizen can be at individual worker level, suggestion system, small group, or large group.
At Toyota, Kaizen usually:
-
Is about local small-scale improvement, e.g. in a work cell, workstation, or business unit ,
-
Involves a small group improving their own work environment and increasing productivity This group is often guided through the Kaizen process by a line manager or team supervisor (in some cases this is the main responsibility of a line manager or supervisor).
On a broad, cross-departmental scale within an organisation Kaizen contributes in quality management, frees up human resources by improving productivity using technology-related solutions, such as process automation, using software tools such as MS Excel, MS Access, etc.
While practising Kaizen at Toyota usually results in small-scale, incremental improvements, the cumulative effect of combining the culture of continual improvement and standardised work yields large results in terms of overall improvement in productivity.
-
This philosophy differs from the "command and control" improvement programs (e.g., Business Process Improvement) of the mid-20th century.
The Kaizen problem-solving and continuous framework follows the PDCA cycle of:
-
Planning to make a change
-
Doing, i.e. making the change
-
Checking, measuring, and analysing the results
-
Acting based on lessons learned from making the change, by comparing actual vs. planned results and adjusting/ fine-tuning the change.
Large-scale pre-planning and extensive project scheduling are replaced by smaller-scale designed and planned experiments, which can be rapidly adapted as new improvements are suggested.
In modern usage, Kaizen is practised in the form of workshops which:
· May last between a few hours to a few days
· Are designed to address a particular issue over the course of a (5-day) week
· Are referred to as "Kaizen blitz" or "Kaizen events".
Kaizen events are limited in both time, scope, and resources. Issues that arise from them are typically solved in later Kaizen blitzes.
In the 21st century, business consultants have adopted the Kaizen framework, tools and techniques to help their clients improve their business processes.
​
General Course Information
​
For general course information please click on the link here.
​
N.B. Please read our Terms & Conditions (T&Cs) and ask for clarifications, if any, before booking your training event.
​
Book now to reserve an on-site or online instructor-led training event of your choice.
​
For more details about our:
-
List of training courses please click here.
-
Consulting services please click here
-
Workshops please click here.
​
For queries, including non-obligation quotes, please contact us.
​
