Overview
The 5-day Lead Auditor training course aims to provide participants with the knowledge, and develop the skills and expertise necessary to:
-
Audit a Quality Management System (QMS) based on ISO 9001:2015
-
Ensure that the organization is competent in maintaining and continually improving its QMS
-
Perform third party audits by applying widely recognized audit principles, procedures and techniques
-
Proficiently plan and perform internal and external audits in compliance with ISO 19011 and the certification process according to ISO 17021.
-
Manage audit teams and audit programmes, communicate with customers, resolve conflicts, etc.
Based on practical exercises, the participants will master the audit tools and techniques.
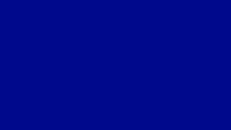
ISO 13485: 2016
Lead Auditor


First time you visit our website?
​
Empower Your Team with Industry-Leading Training Programs
Tailored corporate training for leadership, technical skills and professional development
​
-
We serve corporate clients investing in peoples' knowledge, skills, and competencies, to improve business performance, enhance process, product and service quality, and achieve sustained growth and profitability.
-
We understand the meaning of the business terms "Voice of the Customer" and what constitutes "value" from the customer's point of view.
-
We also understand the difference between "value" and "waste" from the business and individual learner point of view.
-
-
We care about the people, the knowledge enhancement of which is entrusted to us by their organisation or themselves.
-
We focus on learning (not just on training, and issuing certificates) and providing post-training advice and support through workshops and consulting services.
Stratos Lazaridis
CEO The Marvel Academy
Corporate Training Solutions
Mob: +44 (0)749 114 7156
Contents
-
Overview
-
Who should attend
-
Learning objectives
-
Course agenda and content
-
Prerequisites
- Training approach
- Examination
- Competence domains being tested
- Certification
-
General course information
​
​
Lean Leader
​
Overview
​
Lean management is the most effective leadership approach in knowledge-based business environments.
This 3-day course is about Lean leadership, management and culture, aligned with the "Toyota Way" and its application in the Lean Enterprise. By adopting the philosophy, principles, tools and techniques covered in this course, your organisation will gradually progress from its current state and culture to the Lean Thinking way of planning, managing, and optimise its effectiveness and overall performance.
​
Who Should Attend
​
This course is recommended for managers, supervisors, team leader, and business owners aiming to improve the overall performance and competitiveness of their organisation.
Learning Objectives
​
To understand the following:
-
How to lead the cultural change process in your organisation
-
Concepts, approach, and methods required for effective leadership in a knowledge-based business environment
- How to design a Lean management system and structure to enable continuous business, process, product, and service improvement
Training Course details
​
-
3 days (09.00 - 17.00 GMT)
-
Online instructor-led via zoom.us
-
£690 + VAT per delegate
-
Deadline for payment/ registration: 2 calendar days before course start
-
Included: 3 days online instructor-led training, delegate workbook, online exam, and certificate.
​
Onsite training
Please refer to our Terms & Conditions:
-
Trainer's expenses for onsite training, paid by the client
-
Fixed onsite training expenses policy
-
The interrelationship between the various elements of Lean leadership and meeting the needs and requirements of business stakeholders.
-
How to contribute in the efforts of your organisation towards making processes simpler, better, faster, and cheaper to operate without sacrificing product or service quality.
​​​On course completion delegates should be able to:
-
Identify and eliminate waste in day-to-day operational activities
-
Organise, lead, and engage Lean teams in an on-going process of continuous improvement (kaizen).
-
Implement a lean culture based on the philosophy, principles and steps of the "Toyota Way"
-
Apply problem-solving methods employed in continuous improvement
Course Content
​
The course syllabus consists of 6 modules, delivered over three training days:
-
Introduction
-
House of Lean
-
The principles and practices of the Lean culture
-
The role of the Lean Leader
-
The roadmap to becoming a Lean Enterprise
-
Team Kata and the habits of continuous improvement.
​
Prerequisites
​
Proficiency in the English language, willingness to learn, and open mind to new ways of working.
​
Training Approach
​
The course covers both theory and practice:
-
Slide-based training sessions, supported by examples
-
Preparation for the Foundation exam
-
Practice test (mock exam) simulating the certification exam.
​
Examination
​
Upon completion of the training course, you can sit for the exam and become Certified Lean Leader.
​
Exam details:
-
Duration 90 min.
-
Format Closed book
-
Questions 60 multiple choice
-
Pass mark 70% (42 correct answers).
Competence Domains Being Tested
​
The exam covers the following domains:
-
Lean leadership
-
Lean management
-
Lean culture.
​
Certification
​
The Lean Leader certificate will be issued to delegates passing the exam.
​
General Course Information
​
For general course information please click on the link here.
​
N.B. Please read our Terms & Conditions (T&Cs) and ask for clarifications, if any, before booking your training event.
​
Book now to reserve an on-site or online instructor-led training event of your choice.
​
For more details about our:
-
List of training courses please click here.
-
Consulting services please click here
-
Workshops please click here.
​
For queries, including non-obligation quotes, please contact us.
​
​