Overview
The 5-day Lead Auditor training course aims to provide participants with the knowledge, and develop the skills and expertise necessary to:
-
Audit a Quality Management System (QMS) based on ISO 9001:2015
-
Ensure that the organization is competent in maintaining and continually improving its QMS
-
Perform third party audits by applying widely recognized audit principles, procedures and techniques
-
Proficiently plan and perform internal and external audits in compliance with ISO 19011 and the certification process according to ISO 17021.
-
Manage audit teams and audit programmes, communicate with customers, resolve conflicts, etc.
Based on practical exercises, the participants will master the audit tools and techniques.
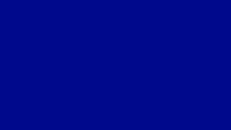
ISO 13485: 2016
Lead Auditor


First time you visit our website?
​
Empower Your Team with Industry-Leading Training Programs
Tailored corporate training for leadership, technical skills and professional development
​
-
We serve corporate clients investing in peoples' knowledge, skills, and competencies, to improve business performance, enhance process, product and service quality, and achieve sustained growth and profitability.
-
We understand the meaning of the business terms "Voice of the Customer" and what constitutes "value" from the customer's point of view.
-
We also understand the difference between "value" and "waste" from the business and individual learner point of view.
-
-
We care about the people, the knowledge enhancement of which is entrusted to us by their organisation or themselves.
-
We focus on learning (not just on training, and issuing certificates) and providing post-training advice and support through workshops and consulting services.
Stratos Lazaridis
CEO The Marvel Academy
Corporate Training Solutions
Mob: +44 (0)749 114 7156
Contents
-
Overview
-
The role of the LSS Yellow Belt
-
LSS Yellow Belt training
-
Purpose
-
Objectives
-
Who should attend
-
Benefits for the organisation
-
Benefits for individual learners
-
Syllabus
-
Course content
-
Prerequisites
- Training approach
- Examination
- Certification
-
General course information
​
​
Lean Six Sigma Yellow Belt
​
Overview
The Lean Six Sigma Yellow Belt (LSS YB) training is designed to provide delegates with a good understanding of the basics of Lean Thinking/ Lean Manufacturing and Six Sigma regarding the following elements of each practice:
-
Brief history
-
Philosophy
-
Methodology
-
Basic LSS tools and techniques (toolbox).
Lean Six Sigma
Yellow Belt (LSS YB)
Part 1 of LSS Green Belt
Training Course details
-
2 days (09.00 - 17.00 GMT)
-
Online instructor-led via zoom.us
-
£490 + VAT per delegate
-
Included: 2 days online instructor-led training, delegate workbook, online exam, and certificate
-
Prerequisite: completing Yellow Belt training is mandatory before attending Green Belt raining.
​
For an overview of the LSS DMAIC methodology, please click here.
​
The role of the LSS Yellow Belt
​
Yellow Belts are considered as process, product, or service subject matter experts (SMEs). Although they are not experts in the LSS DMAIC methodology, tools, and techniques they understand:
-
The objectives, activities, deliverables, and basic tools and techniques used during each project stage
-
Key concepts of Team problem-solving.
Yellow Belts are expected to:
-
Improve processes in their own day-to-day work activities
-
Provide Subject Matter Expertise to support Green and Black Belts in managing their projects.
​
LSS Yellow Belt training
The training will prepare the delegates to:
-
Participate as team members/ contributors to LSS projects
-
Start thinking about solving simple problems and making small-scale incremental improvements in their own working area of responsibility.
​​
Following the use of the LSS DMAIC methodology for several months, Yellow Belts can choose to continue their Lean Six Sigma training and professional development by attending the Green Belt training (LSS GB). This will help:
-
Provide a refresher to what they have already learnt as Yellow Belts
-
Develop a better and deeper understanding of the DMAIC methodology
-
Introduce more advanced LSS tools and techniques, including basic statistical process control (SPC) tools.
The Green Belt training also offers the opportunity for certification.
​
Purpose
​
This course has been designed to teach Lean Six Sigma fundamentals and their application in their day-to-day job role, as well as in LSS projects..
Delegates are trained and tested on their understanding and ability to apply basic LSS tools and techniques of the DMAIC improvement methodology.
​
Some tools and techniques are commonly used in both Lean and Six Sigma
-
Other tools and techniques are used exclusively in either of the above disciplines (Lean or Six Sigma)
Objectives
​
To train and develop competent Yellow Belts, capable of contributing as team members to the successful completion of Lean Six Sigma (LSS) projects.
​
Who should attend
Anyone working as team member in LSS process improvement projects.
​
Note: As Black Belts and Green Belts begin their projects, they need team members to perform various roles and complete specific tasks, depending on their “Belt” level of competence. Yellow Belts (YB) form an important part of LSS deployment projects.
​
Benefits for the organisation
​
These include “hard” and “soft” benefits such as:
-
Increase in customer satisfaction and loyalty, resulting in repeat orders and referrals and reduced customer acquisition costs
-
Increase in employee satisfaction, resulting in higher productivity and moral, employee retention and loyalty, and reduced recruitment, and onboarding costs
-
Increase in productivity and effective utilisation of resources
-
Reduction in operating costs
-
Increase in business profits
​
Lean Six Sigma increases your organization’s profits by streamlining its core, management and supporting processes. This streamlining results in value creation and delivery to customers and consumers in the form of products or services.
-
These are produced faster and more effectively, and delivered on time and free of customer-perceptible defects.
​
Lean Six Sigma increases revenue by enabling your organization to do more with less.
-
This includes producing and selling higher quality products or services, meeting customer requirements and value for money, using fewer human and other resources.
Benefits for individual learners
​
Yellow Belts are individuals considered to be problem-solvers and the strategies they use can work in different environments.
-
This level of LSS certification is mainly for beginners, taking their first steps in the corporate world at a participating organization.
​
At the end of the training LSS YB candidates should have learned and understood the following:
-
Basic concepts fundamental to Lean, Six Sigma, and the combined Lean Six Sigma methodology
-
The stages of DMAIC (Define, Measure, Analyse, Improve and Control), the LSS project lifecycle
-
Basic tools and techniques, used in problem-solving and business process improvements
-
The role and responsibilities of the Yellow Belt and the expectations for their participation and contribution in successful completion of LSS projects
-
The essence and importance of the equation y = f(x)
​
They should also be capable and confident in:
-
Applying the above knowledge and understanding in LSS Green Belt and Black Belt projects.
-
Helping solve business issues and contribute in business process improvement.
-
Using process-related data and basic statistics
Syllabus
​
The LSS YB syllabus has been prepared taking into consideration the following international best practices:
-
International Association for Six Sigma Certification (IASSC) Yellow Belt body of knowledge (BoK)
-
American Society for Quality (ASQ) Yellow belt body of knowledge
-
ISO 18404: 2015 standard (Quantitative methods in process improvement - Six Sigma - Competencies for key personnel and their organizations in relation to Six Sigma and Lean implementation).
​
Course Content
​
-
Introduction to Lean, Six Sigma, and Lean Six Sigma (LSS)
-
Hierarchy of "Six Sigma Belts"
-
Business process architecture: core, management, and support processes
-
Process elements and the process equation
-
Key Lean and Six Sigma terms and concepts
-
Three types of value : CVA, BVA (type 1 muda), and NVA (type 2 muda)
-
Key Lean and Six Sigma Metrics
DMAIC: the LSS project lifecycle
-
LSS project selection
-
5 stages of DMAIC: Define, Measure, Analyse, Improve.and Control
-
Benefits realisation
Yellow Belt Tools and Techniques
-
Lean Triad - 5S, Poka Yoke, SMED
-
Voice of the Customer
-
SIPOC diagram
-
Value Stream Terminology
-
Heijunka, the art of production levelling
-
Types of variation
-
Introduction to Statistical Process Control
-
Data and information
-
Process capability and process performance measures
-
Root cause analysis tools
-
Business problem solving: definition & methods, tools & techniques
-
Kaizen Events' types and overview
-
Lean Enterprise and Lean management
​Prerequisites
​
Proficiency in English, willingness to actively participate during the training sessions, and open mind to learn.
​
Course format and duration
​
Duration: typically, on Monday and Tuesday, if combined with Green Belt training; otherwise, as agreed between the client and BT&CS.
​
Examination
The exam is intended to validate student proficiency with Lean Six Sigma tools and techniques.
-
Prerequisites: passing a 15-question quiz (see notes) before sitting the LSS YB certification exam.
-
30 multiple choice questions, one correct answer per question
-
Pass Mark: 70% - min. 21 correct answers.
​
Notes
-
The LSS White Belt (WB) syllabus equivalent is completed in the form of self-study of a document issued by BICT before attending the LSS YB training.
-
The quiz is completed by the delegates attending YB training before sitting the YB exam.
Certification
Candidates passing the exam will be awarded the LSS YB certificate.
Candidates failing the exam can re-take it for a nominal administrative fee of £50.
​
​
For general course information please click on the link here.
​
N.B. Please read our Terms & Conditions (T&Cs) and ask for clarifications, if any, before booking your training event.
​
Book now to reserve an on-site or online instructor-led training event of your choice.
​
For more details about our:
-
List of training courses please click here.
-
Consulting services please click here
-
Workshops please click here.
​
For queries, including non-obligation quotes, please contact us.
​
​
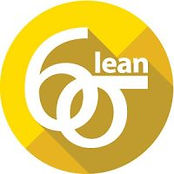

